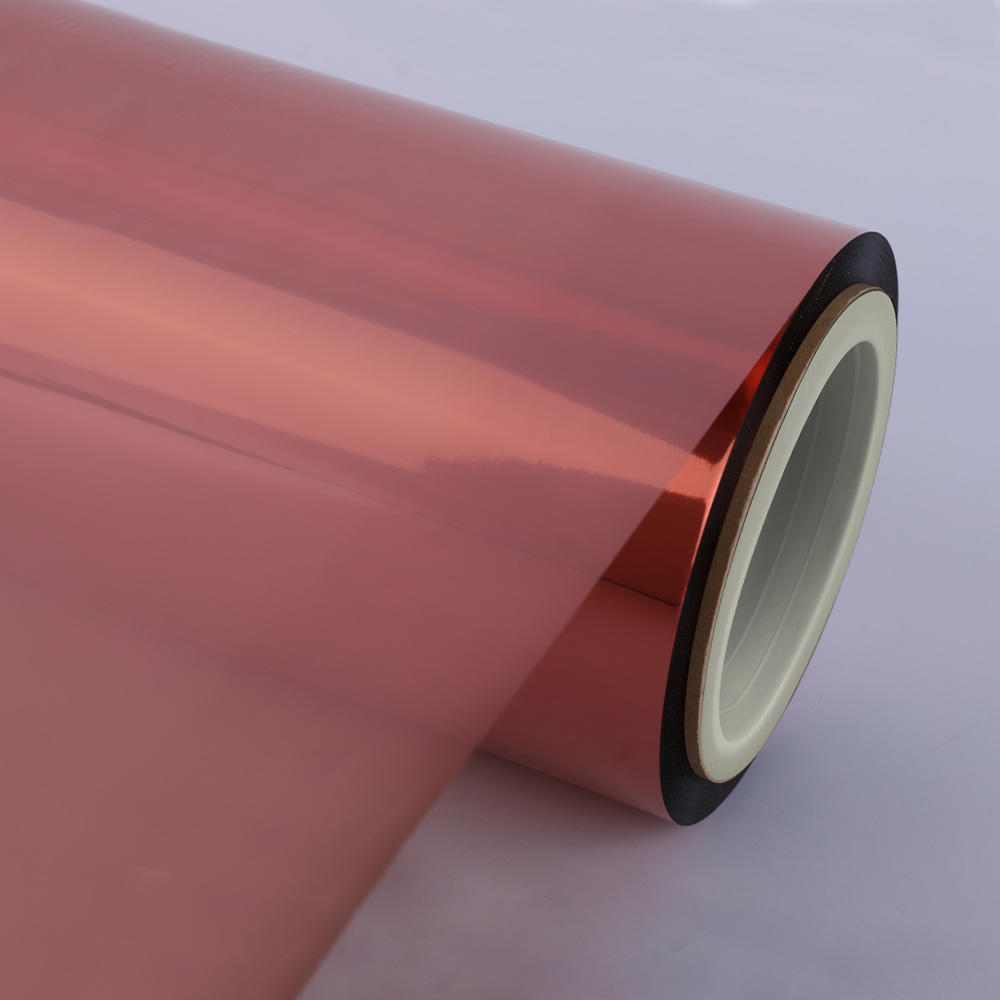
With the continuous improvement of environmental protection requirements, benzene-soluble chlorinated polypropylene inks are gradually eliminated from the market, replaced by polyurethane integrated inks, and polyurethane integrated inks have poor adhesion on BOPP materials, and the tape is printed off the machine. The fastness is relatively poor, and a large area of peeling will occur when the 3M standard tape is used to stick it. Large area transfer of ink can easily occur during peeling detection after compound curing. In view of the poor adhesion of polyurethane integrated ink on
BOPP film, we can take a series of methods to improve it, for example, adding a curing agent to the ink (the amount of curing agent should be less frequently used when adding the curing agent) to form a cross-linked ink layer It reacts to form a large molecular chain, thereby forming a protective film to ensure that the adhesive will not erode the ink layer in a large area and reach the BOPP interface during compounding, and finally peel off the ink from the BOPP film. In addition, the BOPP adhesion promoter can be added to the ink and the surface tension of the corona surface of the BOPP can be increased. The surface tension of the BOPP can be controlled as much as possible above 42dyn. And after many process verifications, BOPP with a thickness of 18um or less has a relatively better effect.