Metallized films are thin polymer films coated on a substrate with a thin layer of flexible metal, more often copper. They provide the sleek metallic look of an aluminum foil at a lower cost and weight. A thin to medium thickness of clear plastic is used to cover the film. To make a metallic one, a dielectric barrier is applied to the film, allowing only a thin to medium layer to form across the barrier. This allows the metal to create the metallic luster. With recent technological advances, it is now possible to produce a large number of these films in the color blue. The blue film can resist impact and will not burn in any way. The only problem is that it is also possible for aluminum to form a puddle on the top layer of the film causing a blue dye effect. This effect is only present when the metallized film is thicker than the barrier properties allow for, which in more cases is around 0.35 mm. The thickness can be increased as the company grows. Metallized film packaging applications have been on the rise for quite some time, particularly where the product is in use, or to be used soon. For example, such applications as medical implants, artificial joints, actuators, tires and compressors are commonly metallically coated to prevent friction and corrosion from damaging the merchandise. In addition, more metals are commonly coated for the same purpose, protecting from impact and rusting to a great extent. Many manufacturers are using a metalized powder coating technique to coat the merchandise in order to increase its durability, weather resistance, gloss and matte finish and reduce weight. Metals such as aluminum, tin, and titanium are commonly used in this technique, although it is possible to coat almore any metal. The more commonly used metal in this technique is titanium, due to its malleability. Titanium pieces are placed in a welding machine that is controlled by a computer, and the pieces are welded at ly high temperature levels. Due to the heat generated, the titanium pieces may often suffer meltdowns during the process, but this is prevented by the ability of the heat to bead into the metal. When the welding is complete, the coated metal will be cooler to touch, which reduces stress levels and increases the likelihood of a flawless weld. One of the main uses of this type of packaging is for thermal and abrasive proofing products, which includes aerospace products. Due to the increase in the growth of the global metallized film market during the forecast period, it is predicted that the markets will continue to expand at an accelerated rate in the coming years.
www.hncypacking.com 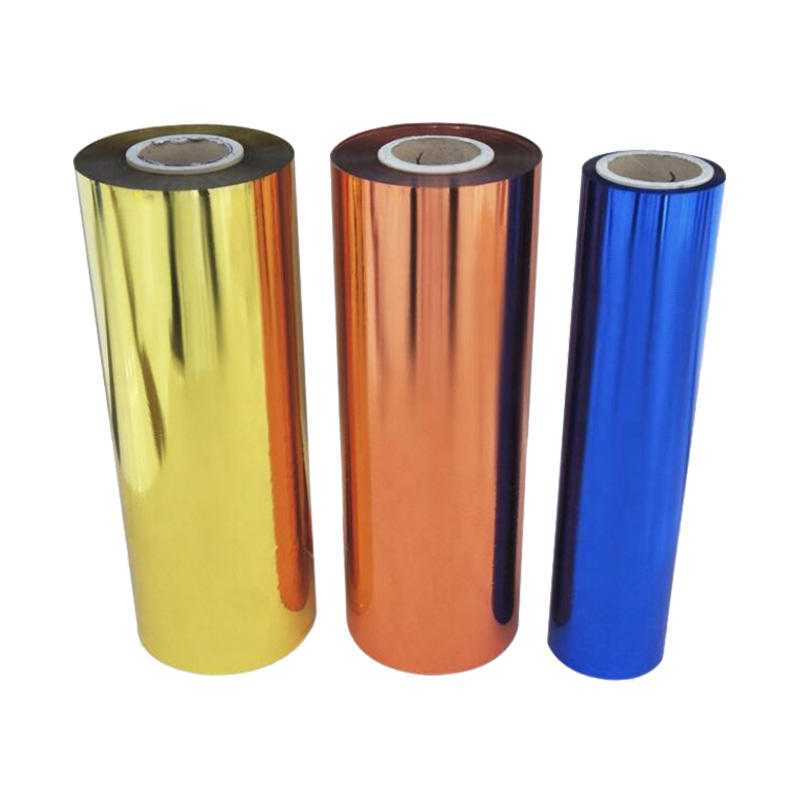